エコプロセス
日本製鉄は、生産活動・製造工程での環境負荷を低減します。限りあるエネルギーを、すべてのプロセスで無駄なく利用する努力を続けています。
副生ガスのリサイクル率
製鉄所内で発生する副生ガスはすべて所内エネルギー源として活用
蒸気生産の排熱利用率
製鉄所内で様々な熱源となる蒸気の75%は燃料を使わず排熱により生産
自家発電の所内発生エネルギー利用率
自家発電の70%は排熱や副生ガス等の所内発生エネルギーを活用
地域社会への電力供給
当社グループでつくった電力のうち37%を地域社会へ供給
当社の代替燃料の使用割合は以下の通りです。
※スマートフォンでは、横にスワイプしてご利用ください。
2016年度 | 2017年度 | 2018年度 | 2019年度 | 2020年度 | 2021年度 | 2022年度 | 2023年度 | |
---|---|---|---|---|---|---|---|---|
代替燃料の使用割合 | 81% | 78% | 81% | 81% | 72% | 75% | 72% | 70% |
自家発電に占める副生ガスと排熱回収による発電の割合
当社は、海外で採掘された鉄鉱石や、鉄鉱石を還元するためのコークスの原料になる石炭、社会から発生した鉄スクラップを主な原料として、鉄鋼製品を生産しています。
石炭を無酸素状態で熱分解してコークスを製造する際に発生するコークス炉ガス、及び高炉から発生する高炉ガス等の副生ガスを、鋼材加熱用の燃料ガスや製鉄所構内にある発電所のエネルギー源として、100%有効に活用しています。
また、製鉄所で使用する電力の殆どが自家発電で、そのうち大部分は排熱及び副生ガスなどの所内発生エネルギーにより賄っています。このように、製鉄所内で発生するエネルギーを無駄なく活用することで、CO2排出量の削減に努めています。
一方、高温、高圧で操業する製鉄プロセスを活用して、社会や他産業で発生する様々な廃棄物の利用拡大にも取り組んでおり、近年では、廃プラスチック等を積極的に再資源化しています。従来埋め立てや焼却処理されていたこれらの廃棄物を製鉄プロセスにおける原料やエネルギーとして活用することで、CO2の削減に寄与しています。
* 共同火力、関連電炉を含む。
独立発電事業(IPP)でのバイオ燃料使用によるCO2削減
東日本製鉄所 鹿島地区では、2007年に操業を開始した50万kWの発電所にて、構内で発生する梱包用木材パレットをチップ化した廃木材等を石炭代替燃料として使用しています。
2023年度は3,610トンのコーヒーかす・木材チップを使用し、約2,317トンのCO2を削減しました。
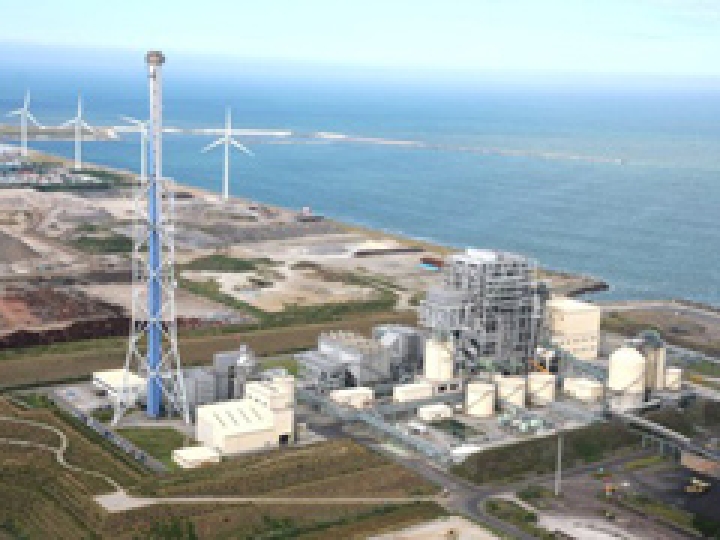
鹿島火力発電所
北日本製鉄所 釜石地区では、木を伐採した後に残る枝葉・梢端部分や間伐材など、林地残材を「バイオマスエネルギー」として活用し同時に森林整備にも貢献しています。
2023年度は木質バイオマスを発電用に年間24,879トン使用し、約26,700トン/年のCO2を削減しました。
2016年 新エネ大賞 経済産業大臣賞(㈱IHIと共同受賞)
2023年(令和5年度)市村地球環境産業賞 功績賞(㈱IHIと共同受賞)
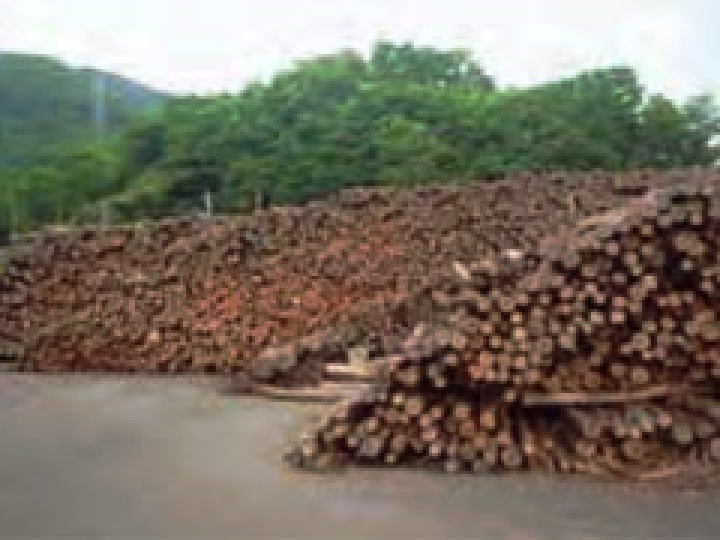
木質バイオマス(北日本製鉄所 釜石地区)
九州製鉄所 大分地区では、2014年度から発電用に木質バイオマスの使用を開始し、2023年度は年間5,242トン使用し、約8,759トン/年のCO2を削減しました。
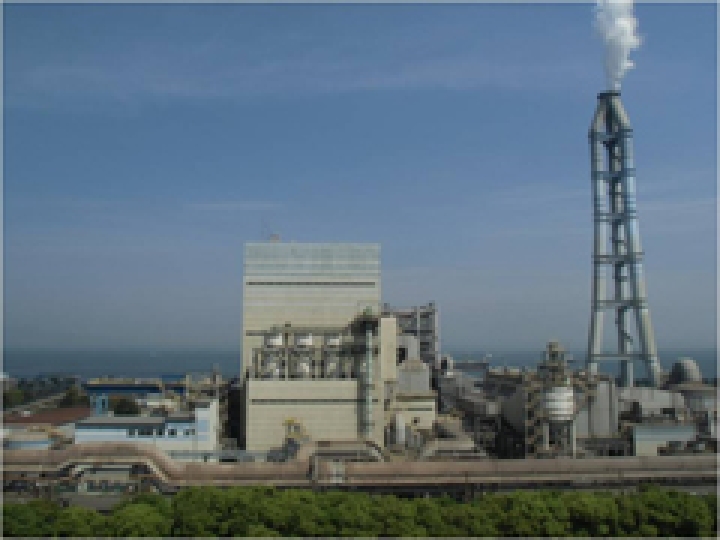
発電所全景
高炉のエネルギー効率改善への取り組み
高炉は炭素を還元剤として鉄鉱石から酸素を取り除く還元反応を行うプロセスです。当社は高炉の大型化や安定操業によるエネルギー効率改善、高炉炉頂圧による発電等、様々な技術を開発・導入し、世界最高レベルの省エネ・省CO2化を実現しています。
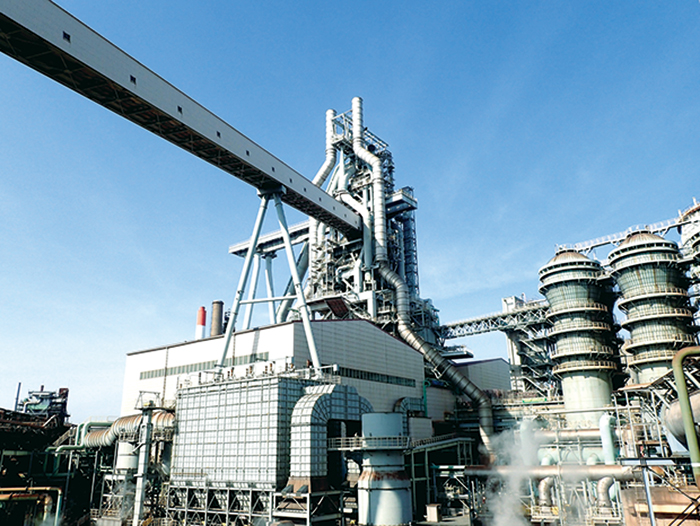
関西製鉄所第2高炉
大規模排熱回収 コークス乾式消火設備(CDQ)
CDQではコークス炉でつくられた赤熱コークスを不活性ガスで冷却し、その熱で発電用蒸気を発生させることで、旧来の湿式消火方式に比べて40%の省エネルギーを実現しています。1976年の九州製鉄所八幡地区での1号機建設以降、全国の製鉄所に設置されており、海外への技術移転も進められています。
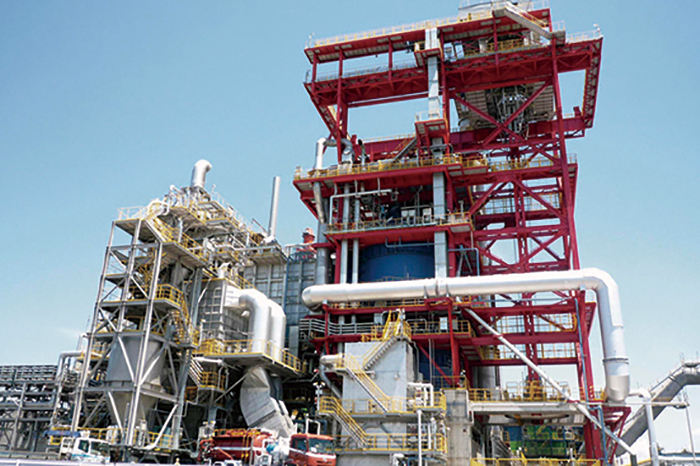
CDQ
リジェネバーナーの導入
対になった2つのバーナーで吸熱・加熱を交互に行う加熱炉により排ガス顕熱を有効利用して高温の予熱空気が得られる燃焼方式で、従来に比べ4分の1の省エネルギーを実現するとともに、低NOx化等の環境対策の面で非常に優れています。
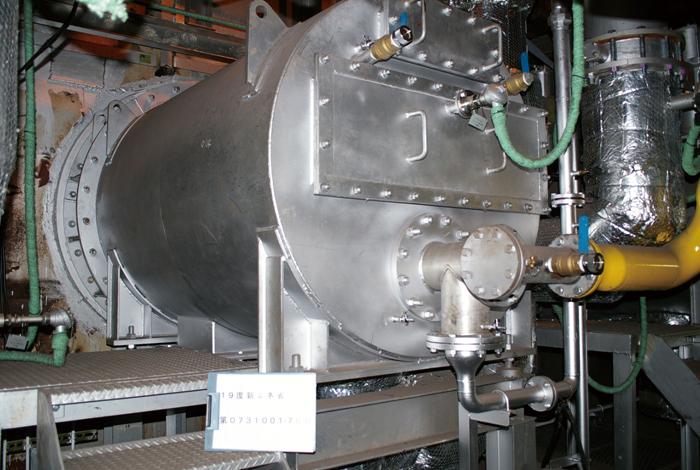
リジェネバーナー
安定生産のための基盤整備(「つくる力」の継続強化)
主力製鉄所が操業開始から約50年を経過し従業員の世代交代も進展するなか、当社ではトラブル等による減産や効率低下を防ぎ安定生産を実現するため、設備の改修・更新・新設等のハード対策や、ノウハウの標準化・人材育成・全社エキスパート活動(特定課題解決のための全社知見の活用)等のソフト対策を進めています。
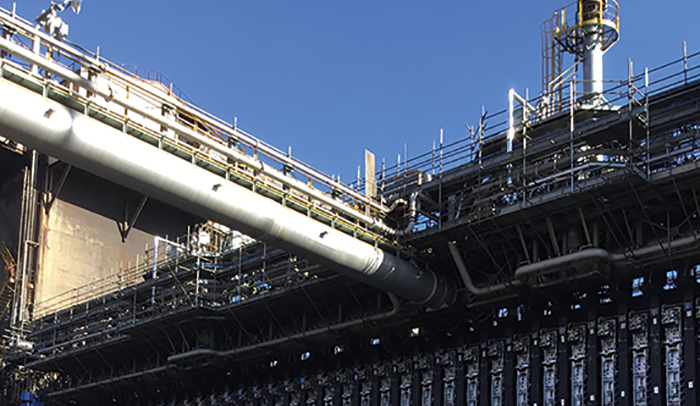
北日本製鉄所 室蘭地区5コークス炉リフレッシュ