Quality-related initiatives
Quality management is one of the most important aspects in obtaining the trust and satisfaction of customers in the provision of products and services. All of our relevant employees are responsible for thorough quality management. In coordination with product units and individual steelworks, the Company’s Quality Assurance Department promotes measures to cope with Groupwide quality control and assurance issues.
Nippon Steel Group’s quality assurance system
Nippon Steel’s quality assurance system is based on autonomous quality management activities at individual steelworks, product units, and Group companies in Japan and abroad.
The Quality Management Division, in cooperation with the steelworks and Product Units, promotes quality compliance education, behavioral risk reduction activities, and the identification and mitigation of quality risks through quality audits. The code of conduct for quality, called the five basic rules of quality behavior, has been made known to all employees, with a focus on improving the awareness in quality compliance and preventing quality problems to occur. Information on quality-related events is promptly shared across the Group and at appropriate times measures are launched to resolve issues through standardization, systemization, and automatization. These measures are then implemented to enhance identification management of actual products to improve reliability of testing and inspection.
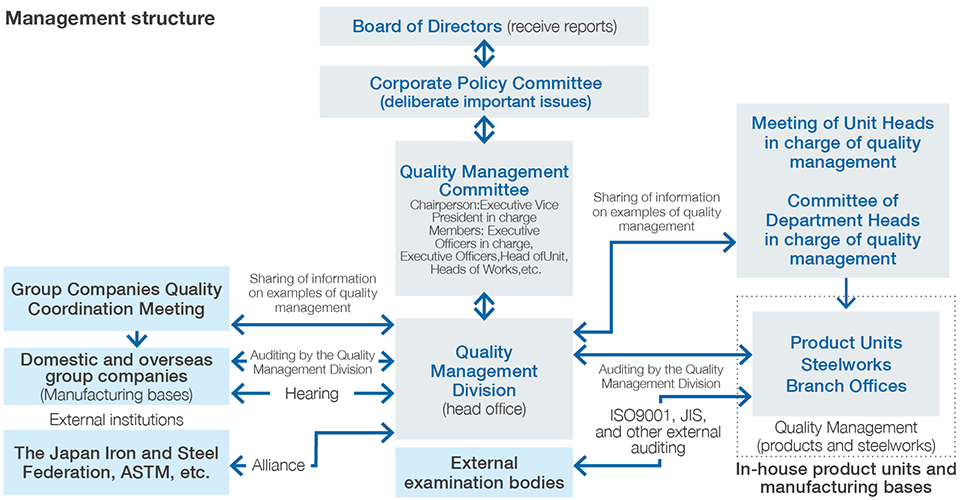
Guide to the Five Basic Rules
of Quality Behavior
Quality auditing by the Quality
Management Division
Nippon Steel Group's basic quality management policy
In line with the Japan Iron and Steel Federation's Guideline toward the enhancement of quality assurance system, we are promoting the enhancement of education on quality compliance (compliance with laws and regulations) and activities to reduce quality risks and implementing a basic policy of identifying quality risks through quality audits throughout the Group.
Quality management issues are shared by the Quality Management Committee, chaired by the Executive Vice President. By having the Committee review actions to take for resolving the issues, we strive to maintain and improve our quality management system.
Activities aimed at strengthening the quality assurance system of the Nippon Steel Group
- Education on quality compliance
Employees of the Company and the Group companies receive quality compliance education. It covers such topics as the importance of compliance with laws and regulations, the impact that our products and work have on society, quality risk management, and internal rules and standards. This education takes the form of training that effectively uses quality e-learning and digital tools.
- Activities to reduce behavioral risks
Based on the analysis of the causes of past quality issues, we have established the basic principles that employee involved in quality management should follow and are working to disseminate them as the Five Basic Rules of Quality Behavior. To improve reliability of testing and inspection, we also work to eliminate risks from human intervention by automating data retrieval and introducing systems for product identification and product quality judgment before shipment.
- Quality audits
The Quality Management Division performs periodic quality audits of the Company and the Group to enhance customer confidence. Audits include a review of compliance with the Japan Iron and Steel Federation’s Guideline, conformity with standards and specifications, and quality-related behavioral risks. We are nurturing auditors at steelworks and Group companies to strengthen the autonomous audit system. We also receive external reviews, such as those for ISO 9001 and JIS certifications, to raise the credibility of our quality management system.
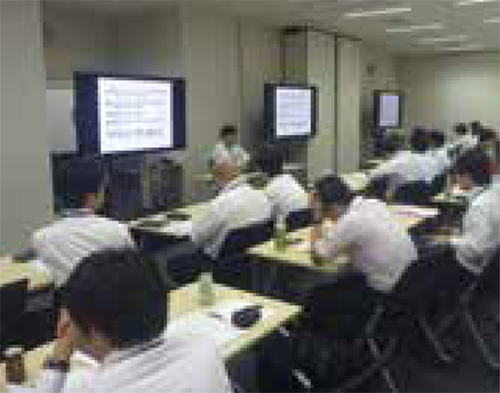
Basic training on quality management
Quality management system and standardization activities
Quality management system (ISO 9001 certification)
All steelworks of Nippon Steel are ISO 9001 certified. By implementing the quality management system, we ensure that the processes used to provide products and services to customers are appropriately managed.
Following the reorganization of our manufacturing bases in Japan, we are integrating the quality management systems, which have been individually certified at the steelworks or area level. Once completed, the integration will enable each steelworks to clarify their quality policy and to accelerate their continuous quality improvement activities.
Standardization activities
With regard to Japanese and international steel standards (JIS, ISO, and ASTM), we promote the establishment and revision of standards by participating in the standardization activities led by the Japan Iron and Steel Federation and contribute to the standardization (rules development) of steel products through public-private cooperation. Building systems for standardization also helps us nurture human resources specialized in standardization.