Carbon Neutral Vision 2050
When Nippon Steel announced its Carbon Neutral Vision 2050 in March 2021, the Company positioned climate change issues as the priority management challenge for the Medium- to Long-Term Management Plan.
We have taken up the challenge to achieve carbon neutrality in 2050, and are striving to reduce CO2 in our value chain by providing two types of value: by providing high-performance steel products and solutions that contribute to reducing CO2 emissions throughout society, and by providing carbon neutral steel through decarbonization of the steelmaking process.
Related materials
Nippon Steel’s GX Initiatives 2025(191KB)
[Short version] 30 seconds
[Long version] About 6.5 minutes
Providing two type of values targeted by the Carbon Neutral Vision 2050
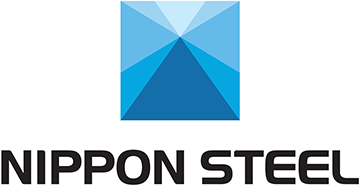
In support of the ambitious government policy to realize a carbon neutral society in 2050, we announced the Carbon Neutral Vision 2050 as a part of the Medium- to Long-Term Management Plan in March 2021.
Decarbonization of steelmaking process for providing carbon neutral steel
We have formulated a target of reducing total CO2 emissions by 30% by 2030, compared to the 2013 baseline and of achieving carbon neutrality in 2050. We are working to develop and actually implement breakthrough technologies in steelmaking process ahead of steel companies in other countries.
Our plan is ambitious compared to those of our global peers, and is intended to significantly contribute to the Japanese government’s plan. With the assistance of the Green Innovation Fund1, we are working on specific plans of the roadmap of development and practical implementation.
1 Commissioned and grant projects of New Energy and Industrial Technology Development Organization (NEDO), which supports companies to carry out projects aimed at achieving ambitious targets for 2030 in focused areas of the Japanese Government’s Green Growth Strategy, such as CO2 emission reduction.
2030 Target
30% or more reduction in total CO2 emissions vs. 2013
Vision 2050
Ambition to become carbon neutral
[Scope of scenario]
Domestic
SCOPE 1+2 (direct emissions in our production sites + indirect emissions from purchased electricity)
4 Including Nippon Coke & Engineering Co., Ltd. and Sanso Center Co., Ltd.
Carbon neutral steel production process (conceptual)
In the current BF-BOF and EAF processes, coal (coke) has been utilized as 1) a reducing agent, 2) a source of heat, and 3) plays a role to support the function of raw materials at high temperature in a solid form while facilitating to maintain ventilation in the furnace. However, CO2 is inevitably generated during the reduction reaction.
We are therefore drastically reviewing the process. As our top management issue, we are developing and implementing the following three breakthrough technologies: 1) Reduction with hydrogen in BFs (injecting hydrogen into existing BFs for partial replacement of carbon use), 2) Hydrogen direct reduction of iron (producing solid reduced iron by hydrogen reduction in direct reduction furnaces (DRFs) ), and 3) High-grade steel production in large size EAFs (improving the productivity of EAFs to manufacture high-grade steel not producible today using direct reduced iron and steel scrap). In addition, we have started to develop technologies such as high efficiency melting of direct reduced iron using an electric melting furnace.
■Three breakthrough technologies Nippon Steel is challenging
■Three external conditions for which government support is required
For smartphones, please enlarge the figure.
Decarbonization of steelmaking process
High-grade steel production in large size EAF
A new EAF installed in the Setouchi Works Hirohata Area started its commercial operation in October 2022, making it the world’s first integrated EAF steelmaking process that enables the production and supply of high-grade electrical steel sheets. Also, regarding the conversion from the BF-BOF process to the EAF process, we started full-scale studies at two candidate sites, the Kyushu Works Yawata Area and the Setouchi Works Hirohata Area. We began construction of a small EAF (capacity: 10 tons) in the Hasaki R&D Center to start experiments in the second half of fiscal 2024.
Reduction with hydrogen in BFs
Japan’s three blast furnace steelmakers, including Nippon Steel, are jointly developing the COURSE50 blast furnace, designed to replace carbon used in the BF as a reducing agent with hydrogen-rich gases generated in steelworks. This project has already established the technologies that can reduce CO2 emission in a COURSE50 test furnace (12m3).
In February 2023, we decided to conduct demonstration tests at the East Nippon Works Kimitsu Area using the No. 2 BF, a large-scale BF in operation that is approximately 400 times larger than the test furnace. We are installing equipment for the demonstration tests, which are scheduled to begin in fiscal 2026. Since May 2022, we have been developing technologies with the modified COURSE50 test furnace. So far, the test in November-December 2023 has already confirmed the world’s highest 33% reduction in CO2 emission in the blast furnace. We are conducting more demonstration tests to further reduce CO2 emissions by 40% or more.
We are working to establish the Super COURSE50 technology in large BFs (50% or more reduction in CO2 emissions).
Hydrogen direct reduction of iron
we started building a small test furnace in the Hasaki R&D Center to start experiments in fiscal 2025. In order to realize production efficiency that can replace the blast furnace process by using the integrated process of hydrogen direct reduction, electric melting furnace, and converter for low-grade iron ore, we are also starting to develop a technology for high efficiency melting by electric melting furnace utilizing direct reduced iron.
Based on this, by 2040, we aim to solve issues such as utilization of low-grade iron ore and conversion of reduction material from natural gas to hydrogen, and we aim to establish technology for commercializing a direct hydrogen reduction reactor using lowgrade iron ore from Australia and other countries as feedstock.
For smartphones, please enlarge the figure.
Carbon Neutral Vision 2050 TOPICS
The COURSE50 Project*1 The Super COURSE50 Project*2
The COURSE50 is a technology development project that was undertaken from 2008 to 2022 with the aim of partially realizing steel production using hydrogen in the current situation where there is no infrastructure for supplying large amounts of hydrogen.
In the 12m3 test blast furnace constructed in the Kimitsu Area of East Nippon Works, the testing has a target of about a 30% reduction in CO2 emissions: more than 10% by hydrogen reduction using hydrogen contained in the hydrogen-based by-product gas (coke oven gas) generated in the steelworks, and a 20% offset through separation and capture of CO2 from the blast furnace gas. The testing verified more than 10% by hydrogen reduction while, in the case of offset by CO2 capture, we have developed an energy-saving technology using the chemical absorption method and have already put it into practical use for the industrial use of CO2.
Looking ahead to a time when the social infrastructure for an adequate hydrogen supply is in place, we are undertaking the Super COURSE50, a development project aided by the GI Fund with a technology aimed at further reduction of CO2 emissions (more than 50% reduction) by heating and using hydrogen purchased from outside the steelworks, and by maintaining the thermal balance inside the blast furnace.
The testing began in May 2022, and the project has steadily advanced development, confirming the world’s highest-level reduction of 22% in CO2 emissions from the blast furnace itself.
The subsequent testing in November and December 2023 confirmed a 33% reduction in CO2 emissions from the blast furnace itself, posting a new record for the highest reduction in the world. We are proceeding with verification testing with the goal of reducing emissions by 40% or more in fiscal 2024.
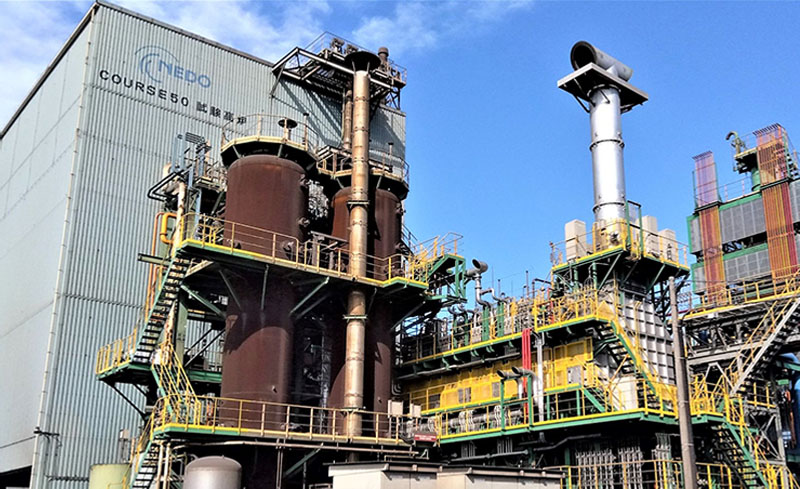
Source: NEDO “Hydrogen utilization in iron and steelmaking processes” project
*1 Commissioned project by the New Energy and Industrial Technology Development Organization (NEDO)
*2 The Green Innovation Fund “Hydrogen utilization in iron and steelmaking processes” project (NEDO’s R&D outsourcing support and assistance project)
Development of high efficiency melting and other technologies by electric melting furnace using direct reduced iron (GI Fund)
Nippon Steel has begun research and development on hydrogen reduction steelmaking technology using an electric melting furnace, which was selected as a new theme of the GI Fund‘s “Hydrogen utilization in iron and steelmaking processes” project.
The structure of the electric melting furnace enables continuous hot metal tapping by continuous operation, similar to the blast furnace, and removal of impurities by continuous discharge of slag. In an integrated process from direct hydrogen reduction to electric melting furnace and converter, this steelmaking process may enable both high quality and high productivity even when low-grade iron ore is used.
By establishing a technology for direct reduction of lowgrade iron ore, we aim to reduce CO2 emissions.
New Carbon Neutral R&D Center “Hydreams™”
In order to accelerate research and development for the realization of carbon neutrality, we are constructing a new research facility at the Hasaki Research and Development Center (located in Kamisu City, Ibaraki Prefecture).
The name of the site, Hydreams, is derived from Hydrogen Direct Reduced Ironmaking and Electric Arc Multi-purpose Furnaces for Steelmaking.
Hydreams is currently constructing a small test reduction furnace and a small test EAF in order to develop technologies for large EAFs and the production of reduced iron, which is the raw material for these furnaces.
The small test EAF is scheduled to start being used in the second half of fiscal 2024, and the small test reduction furnace, in fiscal 2025.
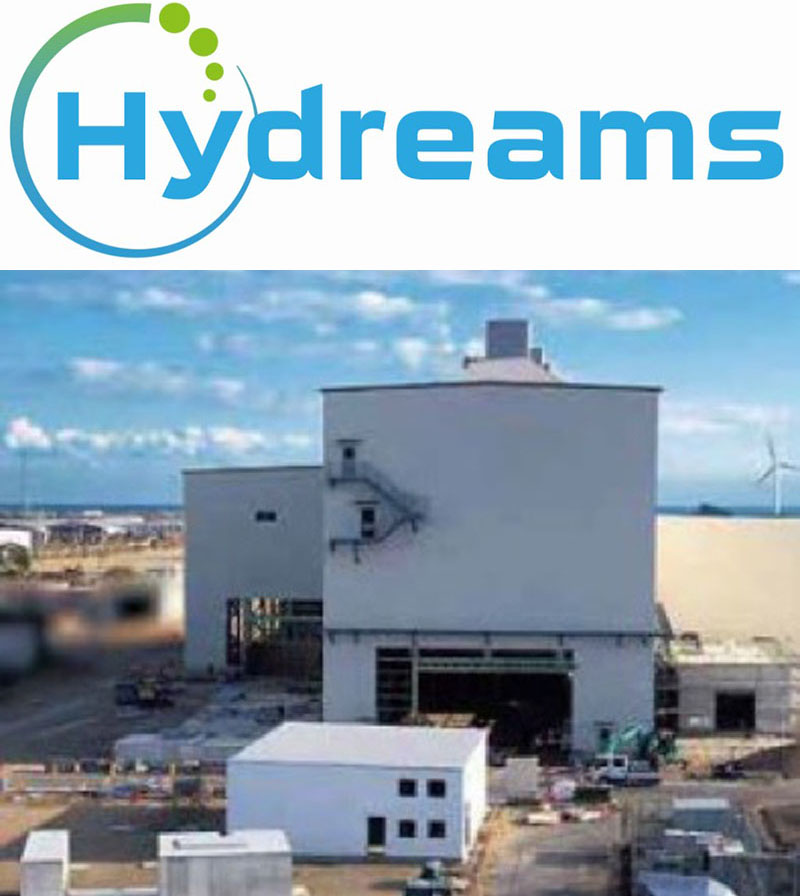
Source: NEDO “Hydrogen utilization in iron and steelmaking processes” project
Three challenges to achieving carbon neutrality in the steel industry
In order to achieve carbon neutrality in the steel industry, there are three unique challenges in technology development, predictability of return on investment, and infrastructure, which must be overcome simultaneously.
Technology Development: the need for the development of breakthrough technologies
Most of the CO2 emitted in the supply chain of the steel industry is from steelmaking processes (Scope 1), particularly in the upstream processes from the reduction of raw materials such as iron ore and scrap to melting and refining.
The steel industry does not have any existing technologies for drastic decarbonization, unlike renewable energy and nuclear power generation in the electric power industry, and electric vehicles in the automotive industry. The industry therefore needs to develop a super-innovative technology that uses hydrogen instead of carbon as a reducing agent for iron ore in the steelmaking process.
Nippon Steel has been striving to develop three breakthrough technologies: “Blast furnace hydrogen reduction,” “reduced iron production using hydrogen,” and “high-grade steel production in large electric arc furnaces” to solve the above-mentioned daunting technical challenges and realize a carbon-neutral steelmaking processes.
Predictability of investment recovery
The development and commercialization of breakthrough technologies that realize carbon-neutral steel production processes require significant R&D expenses and capital investment. At present, in order to achieve carbon neutrality in our steel production processes, we anticipate that we will need to spend more than 500 billion yen in R&D and more than 4 to 5 trillion yen in capital investment on actual equipment by 2050. Operating costs will also increase compared to operating the traditional steelmaking processes.
Concerning R&D expenses, government support via the GI Fund has already been decided. We are making our utmost efforts to become a frontrunner in the world in developing technologies for the practical implementation of the three breakthrough technologies. We are already discovering the seeds of technology and are planning to develop technologies that will minimize significant cost increases. The test results so far have shown steady progress.
With regard to capital investment for practical implementation, predictability of investment recovery is needed in making decisions. In order to ensure predictability, “creation of a market for green steel products” and “sufficient support from the government for rising capital investment and operating costs” are indispensable.
Infrastructure: Energy infrastructure development
Carbon-neutral steelmaking processes require a large amount of hydrogen and electric power, which must be green hydrogen and green power produced without generating CO2. CO2 emissions that would still be partially generated by using Nippon Steel’s three breakthrough technologies must be physically offset by CCUS (Carbon Capture, Utilization, and Storage).
We have positioned the ”stable supply of low-cost green hydrogen and power” and the ”social implementation of CCUS” as ”external conditions that should be established by the government” necessary for carbon-neutral steelmaking processes, and are lobbying relevant government agencies.
Policy proposals and industry activities aimed at overcoming the three challenges
As stated, steelmakers alone cannot achieve carbon neutrality in the steel industry. These are national challenges that should be addressed by the entire nation in cooperation with society, based on (1) policy packages to achieve both international competitiveness of industries and carbon neutrality as well as (2) policies for national strategies that include strong and continuous support, including from the financial side.
To realize these policies, Nippon Steel is determined to take every opportunity to make various proposals on Japan’s climate change measures and energy policies based on the Paris Agreement and to spearhead activities through economic and industry associations.