ECO PROCESS
Nippon Steel is committed to reduction of the environmental impact created by production activities and manufacturing processes. We make continuous efforts in all processes to not waste limited resources and energy.
Recycling rate of by-product gas
All by-product gases generated in the steelworks are used as in-house energy source.
Rate of use of exhaust heat in generation of steam
75% of steam used as various heat sources within steelworks is generated by exhaust heat, with no use of fuel.
Rate of use of in-house generated energy in power generation
In-house generated energy, such as exhaust heat and by-product gas, is used for 70% of in-house power generation.
Supply of electricity to local communities
Supply of 37% of self-generated electricity to local communities
The usage ratio of our alternative fuels is as follows.
On smartphones, swipe sideways to use.
FY2016 | FY2017 | FY2018 | FY2019 | FY2020 | FY2021 | FY2022 | FY2023 | |
---|---|---|---|---|---|---|---|---|
Usage ratio of alternative fuels | 81% | 78% | 81% | 81% | 72% | 75% | 72% | 70% |
Rate of secondary gas power generation and waste heat recovery power generation in-home power generation
As its main raw materials for steel production, Nippon Steel uses iron ore mined overseas, coal as for reduction of iron ore, and scrap generated by society.
By-product gases, such as coke oven gas generated when coal is thermally cracked in an oxygen-free environment in the coke manufacturing process and blast furnace gas generated from blast furnaces, are fully utilized as fuel gas for steel heating furnaces or energy sources for power generation plants on the premises of steelworks.
In addition, Nippon Steel itself generates 91% of the electricity it uses at steelworks, 72% of which is from internally generated energy sources such as waste heat and by-product gases. By not wasting but utilizing energy generated within the steelworks, we do our part to reduce CO2 emissions.
We are also engaged in the recycling of various types of by-products generated by society or other industries by utilizing our steelmaking processes that are carried out at high temperature and high pressure. In recent years, we have been actively recycling waste plastics and other waste materials.
Reuse of these waste, which are traditionally landfilled or incinerated, as raw materials or energy in steelmaking processing is another way that we reduce CO2 emissions.
1 Including cooperative thermal power companis and affiliated electric arc furnaces
Use of bio fuel in independent power production results in CO2 reduction
East Nippon Works Kashima Area’ 500,000 kW Thermal Power Station (an Independent Power Producer or IPP) began operation in 2007 and burns scrap wood chips, which are made from used wood pallets, as an alternative fuel to coal. In fiscal 2023, dregs from coffee making and wood chips, coming to 3,610 tons in total, were used, resulting in a CO2 emission reduction of about 2,317 tons.
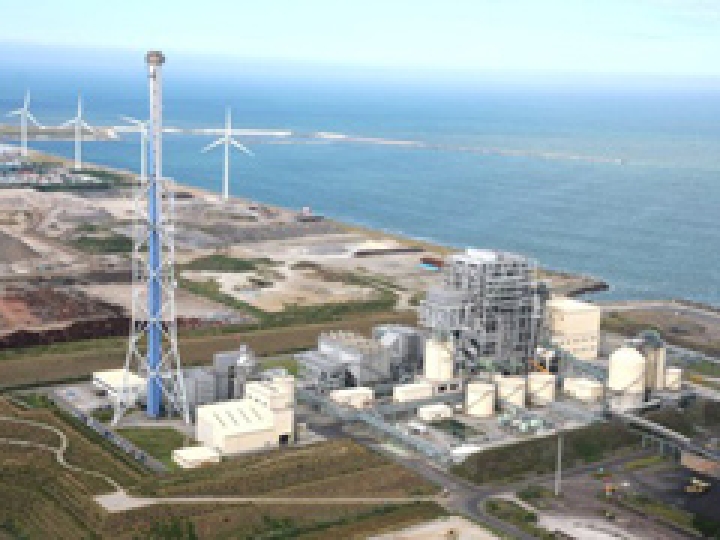
Kashima Thermal Power Station
North Nippon Works Kamaishi area utilizes biomass resources such as leaves, and branches trimmed from lumber trees as biomass energy. This also contributes to forest improvement. In fiscal 2023, woody biomass of 24,879 tons was used, resulting in a CO2 emission reduction of about 26,700 tons.
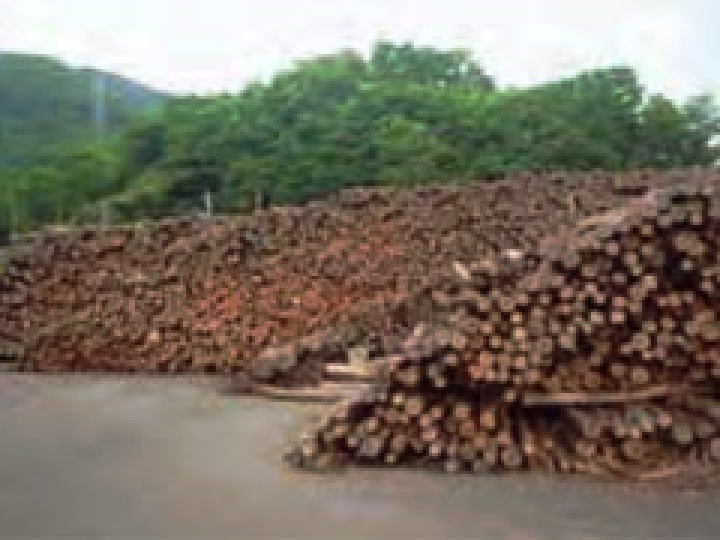
Woody biomass (North Nippon Works Kamaishi area)
Kyushu Works Oita area began using woody biomass for power generation in 2014. In fiscal 2023, it used 5,242 tons per year, resulting in a CO2 emission reduction of about 8,759 tons / year.
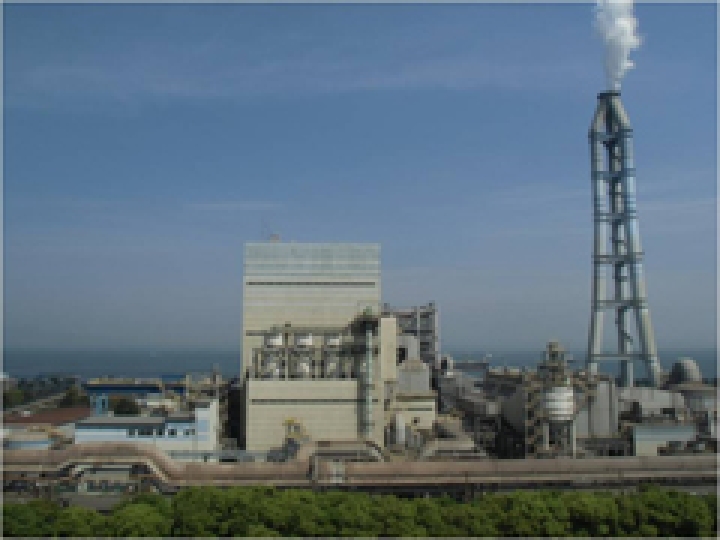
Full view of the power plant
Efforts to improve energy efficiency of blast furnace
In the blast furnace, a reduction reaction to remove oxygen from iron ore, using carbon as a reducing agent, is conducted. Nippon Steel has developed and adopted various technologies, including those to make larger blast furnaces, improve energy efficiency through stable operation, and power generation by use of blast furnace top pressure. These efforts have resulted in realizing the world’s top-class energy conservation and CO2 reduction.
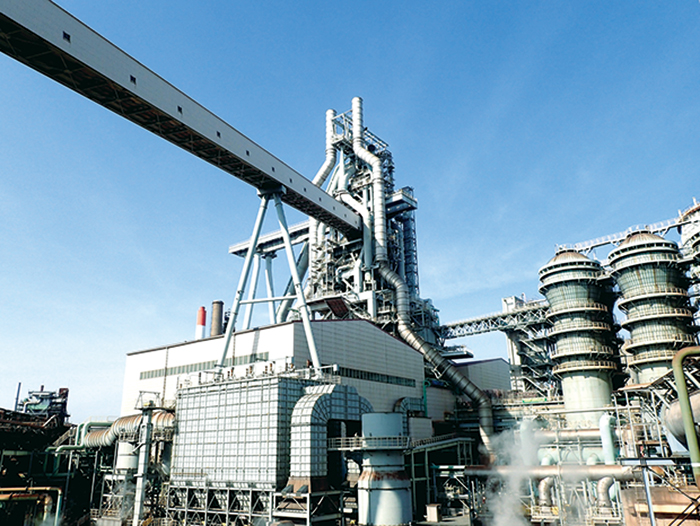
Kansai Works No. 2 blast furnace
Coke Dry Quenching (CDQ) for large-scale waste heat recovery
The CDQ equipment quenches hot coke made in the coke oven with inert gas, and the heat is used to generate steam for power generation. Compared to the conventional wet quenching, 40% energy saving has been achieved. Since the first CDQ unit was installed in the Kyushu Works Yawata Area in 1976, the CDQ equipment has been installed in steelworks nationwide and its technology has been transferred overseas.
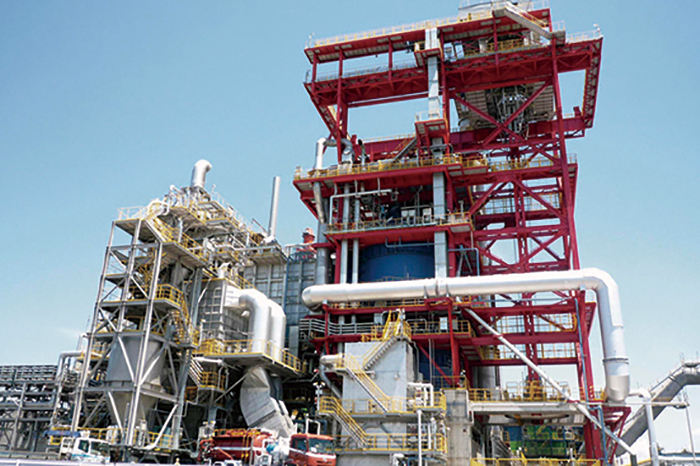
CDQ
Introduction of regenerative burners
A pair of burners alternately heat the air or absorb the heat in the heating furnace, and the exhaust gas heat is effectively used to obtain high-temperature pre-heat air. This combustion system allows to achieve energy savings of one-quarter compared to the conventional system, and also excels in terms of environmental measures such as lower emission of NOx.
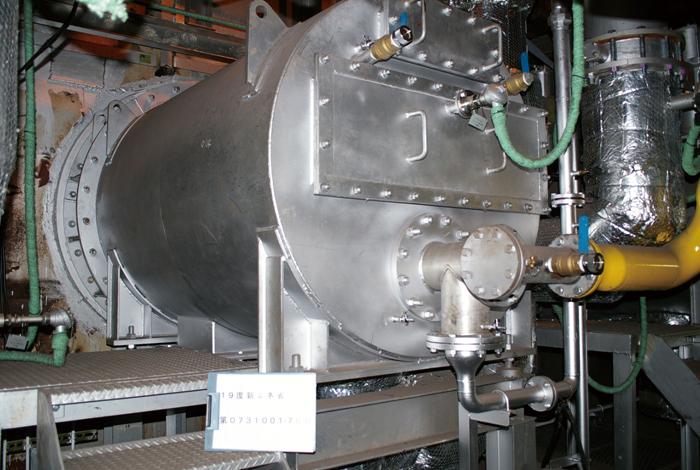
Regenerative burners
Building a foundation for stable production (continued enhancement of strength in manufacturing)
Many of our steelworks are passing about 50-year milestone since the start of their operation. Our workforce is also undergoing drastic generation changes. Against such a background, we are implementing measures in hardware aspects (such as refurbishing, renewal, and new construction of facilities), and in software aspects (such as standardization of know-how, human resource development, and company-wide expert activities aimed at utilizing company-wide know-how to resolve specific issues) in order to prevent production cuts and inefficiencies, caused by problems, and achieve stale production.
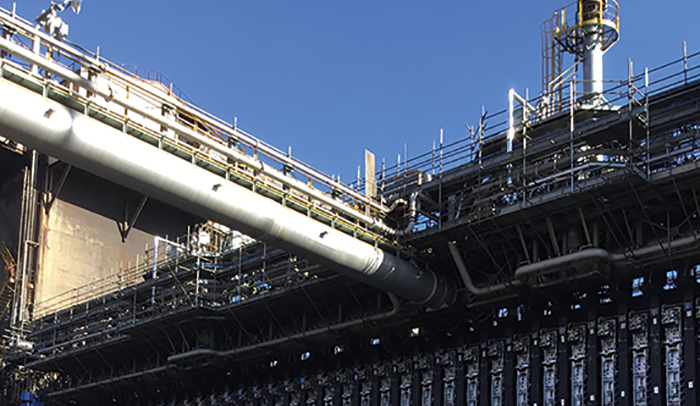
North Nippon Works Muroran area No. 5 coke oven (CO) refurbishment