Safety
In keeping with the basic philosophy that “safety and health of employees of the Nippon Steel Group is the Group’s most important, top-priority values and the basis that supports business development,” the Nippon Steel Group has firmly adhered to its manufacturing values, which include observing the principles of prioritizing safety, protecting the environment, and preventing disasters. We are working on all of the related activities to improve the level of our Occupational Safety and Health Management System (OSHMS) while creating safe and secure workplaces.
The Basic Policy on Safety and Health is applied to Nippon Steel as well as to related or cooperative companies.
Reducing disaster risks to zero, and group-wide sharing of effective measures
We make a risk assessment when planning a new project and regularly conduct safety and risk assessment for existing projects, to prevent accidents and reduce risks. We also seek for greater safety of equipment even when such equipment is essentially safe, and take countermeasures against human error. We also actively promote the use of IT in safety measures, such as checking worker location data via GPS, safety surveillance cameras, and helmet-mounted cameras. We conduct an analysis of actual accidents for the prevention of similar accidents and make known effective examples of accident-preventive measures. As a result of continuing efforts, our safety performance in 2023 shows that the number of accidents accompanied by lost work time was 8 for the company*1, 7 for our cooperating companies (including fatal cases of one for the company and zero for cooperative companies), the comprehensive accident frequency rate was 0.08 (vs. Japan’s steel industry average of 0.81), and the intensity ratio was 0.04 (vs. the same average of 0.12). We will continue to strive for a safe work environment with the safety wellness targets for FY2024 which are zero fatalities/severe accidents and less than 0.10 as the accident frequency rate.

*1 Nippon Steel’s employees include seconded employees as well as temporary and part-time workers, and those dispatched to Nippon Steel.
〔Accident frequency rate〕
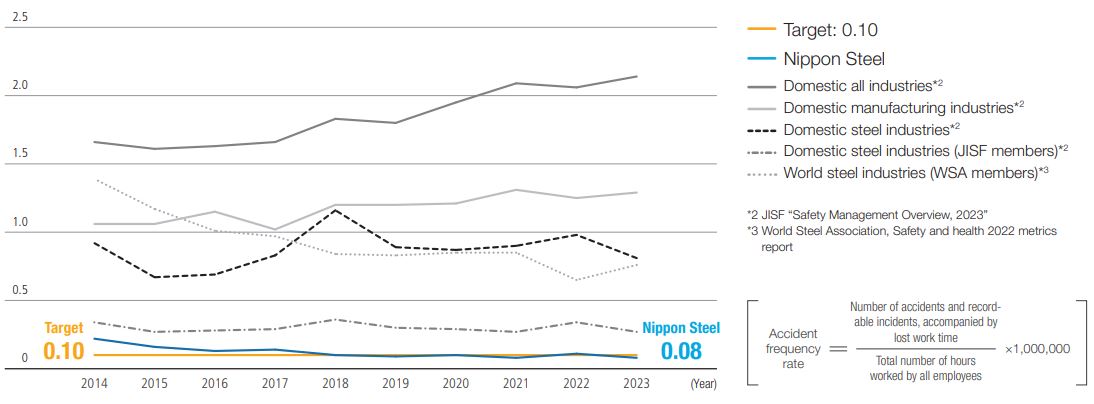
Acquisition of third-party certification
Nippon Steel’s all steelworks acquired the ISO (JIS Q) 45001 Health and Safety certification (published in March 2018) as of April 2024.
Acquisition of ISO (JIS Q) 45001 certificates
FY | |
---|---|
FY2019 | Kansai Works Wakayama Area |
FY2020 | Amagasaki Area and Osaka Area of Kansai Works; Nagoya Works; Kyushu Works Oita Area; East Nippon Works Kashima Area |
FY2021 | Naoetsu Area and Kimitsu Area of East Nippon Works, North Nippon Works Muroran Area, Setouchi Works Hirohata Area |
FY2022 | North Nippon Works Kamaishi Area, Kyushu Works Yawata Area |
FY2023 | Setouchi Works Hanshin Area |
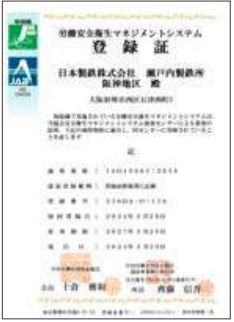
ISO (JIS Q) 45001
Health and Safety certificate
(Setouchi Works Hanshin Area)
Safety training
We make efforts to improve training for accident prevention. The safety training programs are attended by all newly appointed managers of manufacturing worksites (80 managers in fiscal 2021, 65 in fiscal 2022, and 64 in fiscal 2023). Our Taikan Program (an experience-based safety education program) allows employees to experience worksite risk through simulation, so as to better prepare them for anticipating and managing risk. In addition, we regularly hold safety and health education programs (74 participants in fiscal 2022 and, 69 participants in fiscal 2023) for the safety and health staff of our Group companies and major cooperative companies, striving to enhance information sharing about our safety and health management approaches and activities and the acquisition of knowledge about laws and regulations related safety and health.
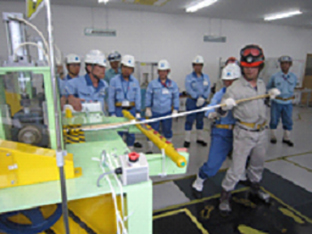
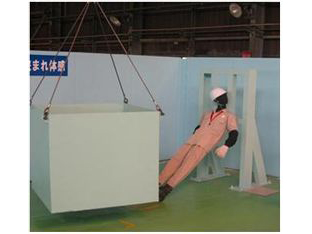
Risk Taikan (Experience-based) Education Program