Research & Development
Nippon Steel is engaged in advancing strategic R&D, aimed at sustainable growth of the Nippon Steel Group
One of the world’s leading research resources
Our R&D resources are among the largest in the world in the steel industry, and we will contribute to the development of society through the R&D aimed at realizing our management plan. Specifically, we will (1) strengthen the development of products with high added value and technology and products that realize carbon neutrality (CN), and (2) acquire a competitive advantage by deploying products and the development technology cultivated in domestic mother mills in the actual site business, and contribute to business expansion for the global system of 100 million tons of crude steel, and (3) work to develop breakthrough steelmaking process to contribute to the realization of CN society. We will also (4) promote the digital transformation (DX) of business operations, including optimization of production plans, and automation of production facilities, by using the vast amount of technical data that we have accumulated over many years and the latest digital technology and AI.
Pillars and contents of medium- to long-term management plan | Representative R&D |
---|---|
|
|
|
|
|
|
|
|
Modern steelmaking in Japan began with iron ore as the raw material at the end of the Edo period and continues to progress today. In recent years, in order to develop products that utilize atomic-level observation technology and advanced calculation science and technology, and to develop manufacturing processes for stably mass-producing them at low cost, various researchers with expertise in materials, physics, chemistry, mathematics, machinery, electricity, information, civil engineering and building construction are active and are participating in a wide range of academic societies both in Japan and overseas. In the middle of the big game change in the decarbonization of society, steel is required to transform from the blast furnace method, which has extremely high production and energy efficiency. On the other hand, there is also a demand for developing products that contribute to the reduction of CO2 in society as inexpensive structural materials. We will use our wide range of specialized technical capabilities and large-scale steel research resources fully for the R&D issues that are required in this era, and we will lead the Japanese industry toward the realization of a carbon-neutral society.
R&D organization
R&D is carried out with the R&D Laboratories as a core. The Steel Research Laboratories are mainly engaged in product development; the Advanced Technology Research Laboratories in discovery of new technology seeds from basic research and R&D related to segment companies; the Process Research Laboratories in process development; and the R&D Laboratories at Steelworks in practical application research. Thus, we are dividing our organization to be in charge of R&D management that contributes to our global management. In addition, we have contributed to the early practical application of developed products and processes in cooperation with Plant Engineering and Facility Management Center, which oversees equipment engineering, and newly-established Plant/Machinery Engineering & Construction Management Center, which is engaged in the design and construction of steelmaking plant facilities. We will promote the development of products and processes for the CN society by utilizing the existing framework of the three laboratories. Furthermore, we will strengthen cooperation with universities and research institutes in the fields that require basic examination, including elemental technologies that our group does not possess.
[R&D organization]
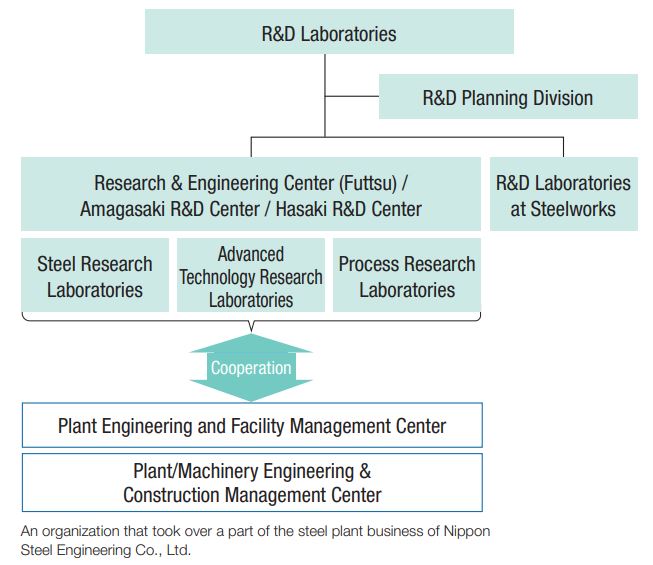
Strengthening products with high-added value and process development
We will continue to work on maximizing the potential of steel as a material, that is, achieving our goal of “mastering steel.” Examples of the development of products with high added value include high corrosion-resistant plated steel sheets (ZEXEED™, etc.), alloyed galvanized sheets (GA), hot-dip aluminum-plated steel sheets (ALSHEET™), nickel-plated steel sheets (SUPERNICKEL™), and grain-oriented electrical steel sheets (GO), non-oriented electrical steel sheets (NO), high-alloy seamless steel pipes. We are promoting this R&D to shift to a more sophisticated order mix.
In process development, we utilize various kinds of large-scale laboratory equipment that can accurately simulate the operation of actual production facilities for each process of ironmaking, steelmaking, and rolling, as well as simulation calculation technology. Thus, we are promoting R&D of highly efficient steelmaking process that considers resources and the global environment in producing higher valued-added products
Next-generation automobiles
We are contributing to the reduction of environmental impact by developing and expanding the application of high-tensile steel sheets to achieve both weight reduction and collision safety of automobiles, developing high-efficiency electrical steel sheets for hybrid and electric vehicles, and improving fuel efficiency through the development of underbody products. We are proposing the NSafe™-AutoConcept ECO3, a next-generation steel automobile concept for the era of carbon neutrality. The cold-forming technology of ultra-high-strength steel sheets, which forms the core of this concept’s processing technology group (NSafe-Form Series), was awarded the “Grand Prize of the Society of Technology of Plasticity” (2023) at the 58th Japan Society for Technology of Plasticity.
[Deepening of high-tensile steel sheets for vehicle body frames]
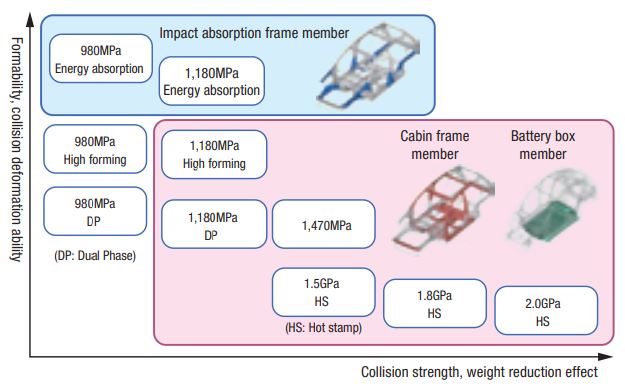
Energy and resources/Shipbuilding
Steel materials for energy and shipbuilding require a quality that ensures long-term safety under various service conditions. We are contributing to improving the safety of final products and enhancing the productivity and competitiveness of customers by supplying high-performance products that utilizes advanced technology.
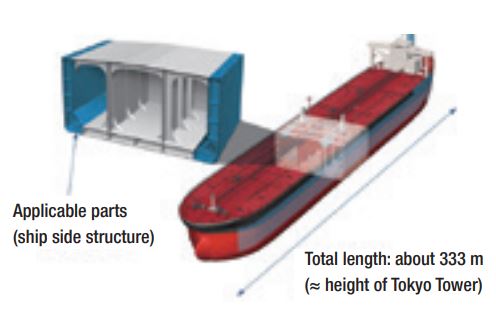
Highly ductile thick steel plate for hull structure superior in collision safety (Nsafe™-Hull)
Challenge of carbon neutrality
We accurately grasp market needs and continuously develop and supply building materials that exhibit our originality. We support social infrastructure such as construction (building pillars and beams) and civil engineering (roads/railways, rivers/harbor, building foundations). As an example of recent years, we have worked on basic research to explain the corrosion mechanism of coating defects in conventional steel materials and found that the addition of a small amount of element (Sn) to steel materials can suppress the elution of iron in a low-pH environment. We developed CORSPACE™, an extended coating cycle steel with excellent LCC, which can reduce the amount of steel corrosion and coating stripped surface in coating defects to about half that of conventional products. Thus, we have received the Excellence Award of the 9th “The Japan Monodzukuri Nippon Grand Awards” (2023) and the Contribution Award of the 55th “The Ichimura Prize in Industry” (2023). The steel materials and their elemental technologies are protected by a total of 78 comprehensively acquired patents.
[Corrosion mechanism of coating defects]
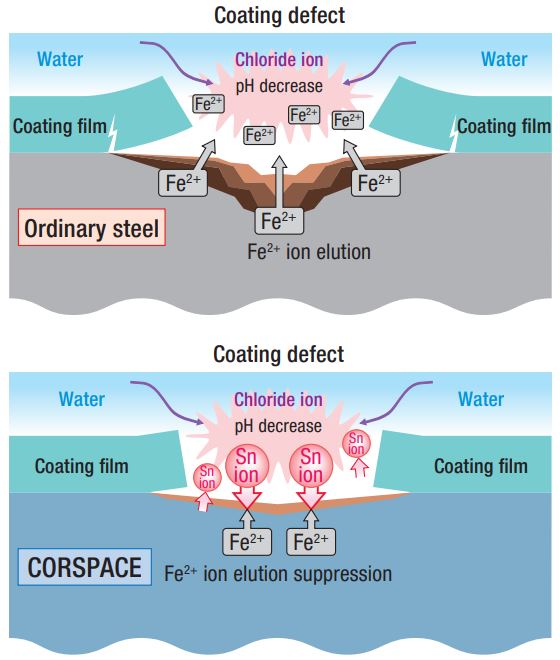
Challenge of carbon neutrality
We aim to achieve carbon neutrality using three breakthrough technologies. “Hydrogen injection into blast furnaces” is an effort to replace the reduction of iron oxide using carbon with hydrogen reduction, and the handling of hydrogen and the decrease in furnace temperature due to hydrogen reduction are issues. “High-grade steel production in large size EAF” is based on the existing technology of the electric furnace, but there are issues in reducing impurities and increasing the size of the equipment. “Hydrogen direct reduction of iron” is a process producing reduced iron from iron ore using a shaft furnace, etc., without using a blast furnace, and there are still issues concerning stabilization of mass production.
Through the Green Innovation (GI) Fund Project of the New Energy and Industrial Technology Development Organization (NEDO), we are tackling these challenges by undertaking demonstration tests using a test blast furnace in East Nippon Works Kimitsu Area and a new test electric furnace and a test shaft furnace at the Hasaki R&D Center (Kamisu City, Ibaraki Prefecture). In 2023, we confirmed the world’s highest 33% CO2 emission reduction at the test furnace, making steady progress in development toward proposing the future steelmaking process. In addition, we will conduct R&D of carbon offset measures such as “NSCarbolex™ Solution” which utilizes steel products that can reduce CO2 during processing and use, and CCUS, etc. We aim for CN with a multi-aspect approach.