News
- Apr. 18, 2025 The civil engineering package has been updated with the addition of “Hat+H (Hat-type sheet pile for Deep excavation)” and “STEEL PIPE PILES with ribs x Sat-in Pile Foundation”.
- Apr. 02, 2025 Designing Metal TranTixxii to be Used in the Largest Quantity in the World on Taiwanese Temple Roof
- Mar. 10, 2025 Nippon Steel Obtained SuMPO EPD Certifications for Pipes and Tubes Used in Chemical Industry and for Boilers
- Dec. 12, 2024 Titanium with Aesthetic Appearance “TranTixxii” Service Life Warranty Launch —Launch of a maximum 150-year warranty through additional extensions—
- Oct. 31, 2024
Launch of the overseas version of ProStruct™, a solution brand for the construction industry
—Expanding the packaged series of steel materials and solution technology to overseas construction markets— - Oct. 30, 2024 Participation in the Japan Pavilion at ADIPEC, the Energy-Related Exhibition in the Middle East
- Oct. 07, 2024 Nippon Steel Obtained SuMPO EPD (Formerly EcoLeaf) Certificationsfor Its Hot Extruded Steel Shapes
- Jul. 10, 2024 Long-term OCTG supply contract with Aker BP renewed –Strengthens strategic partnership through stable supply of OCTG–
- Jul. 03, 2024 Long-term OCTG supply contract with Equinor renewed –Strengthens strategic partnership through stable supply of OCTG–
- Jun. 14, 2024 Acceptance of Orders for High-Alloy Seamless OCTG and Employment of Green Steel “NSCarbolex Neutral” Finalized for CCS to Be Used in Construction Project for Blue Ammonia Manufacturing Plant in the State of Qatar
- May. 15, 2024 Adoption of Coating Cycle Extension Steel “CORSPACE” for the First Time in Overseas ODA Bridge Construction
- Apr. 23, 2024 Participation in OTC, an Energy-Related Exhibition in the U.S.
- Mar. 22, 2024 Designing Titanium TranTixxii wins the European “iF DESIGN AWARD 2024” —The world's first non-ferrous metal material to receive the award—
- Sep. 28, 2023 The Adoption of “NSCarbolex Neutral” steel product for geothermal project in the Netherlands operated by 85 Degrees Renewables.
- Mar. 11, 2022 Nippon Steel's TranTixxii and NIPPON STEEL Stainless Steel Corporation's NSSC220M featured on the roof of an international conference center in Jiangsu, China
- April 22, 2021 Nippon Steel to Launch ZAM®-EX high corrosion resistant coated steel sheets for overseas markets
- Oct. 01, 2020 Our new product "FeLuceTM" (hairline-finished electroplated steel sheet) wins the Good Design Award 2020 ~Our first steel sheet to win the Good Design Award~
- Feb. 14, 2019 NSSMC Receives Shell’s Supplier Award
- Jul. 30, 2018 Execution of Strategic Partnership with BP Oman
- Jul. 30, 2018 "The beauty of distinctive gradations make people feel nature" was posted.
- Jul. 26, 2018 VAM® 21 HT CLEANWELL® DRY ST First Running
- Jul. 19, 2018 Steel Wires Joint Venture Company for Cold Heading and Forging in USA (NSCI) holds an Opening Ceremony
- Jun. 27, 2018 NSSMC and Standard Steel Receive TTX “Excellent Supplier 2017” Award
- May. 29, 2018 NSSMC Named a Top 100 Global Innovator in 2017 for Sixth Consecutive Year
- Apr. 25, 2018 Steel Wires Joint Venture Company for Cold Heading and Forging in USA (NSCI) Starts Commercial Production
- Apr. 17, 2018 Strengthening Supply System for Ultra-high-tensile Steel Sheets New CGL to be installed at Kimitsu Works
- Feb. 27, 2018 Nippon Steel & Sumikin Crankshaft, NSSMC’s manufacturing and sales subsidiary of crankshafts in the U.S., earns Diamond Supplier Award from Navistar
- Aug. 04, 2017 NSSMC’s proprietary titanium product TranTixxii™ is adopted for cladding of a theater in Jiangsu Province, China
Hot Extruded Steel Shapes
Since 1941, the first successful of making steel shapes with hot extrusion using glass lubricants in France, the number of applications for hot extrusion steel shapes has shown remarkable growth in such fields as structural members and machine parts.
NIPPON STEEL installed the hot extrusion plant at its Hikari Works in 1960. Based on the many years of research and development, we have established a sophisticated hot extrusion production system with high-quality steel shapes. Currently, these shapes are highly evaluated by our customers.
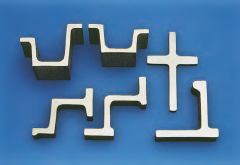
Features
Hot extruded shapes are produced by means of the hot extrusion method. In this method, round billets are heated to around 1,200˚C, and then hot extruded through dies mechanically processed into diverse configurations. The hot extruded shapes thus obtained are then subjected to tensile straightening and other finishing processes to produce the final product.
Accordingly, the hot extrusion process is suitable for producing shapes of complex configuration, multiple-grade / small-lot shapes, and difficult-to-process materials.
Freedom of Design
In contrast to standard specified shapes by rolling process, hot extruded shapes combine both decorative and structural functions that allow the design of structural members that permit optimal originality and freedom in building design.
Save the Machining Process
In contrast to the conventional method by machining (lathe, milling) from material block, the hot extrusion process forms shapes by passing the material through die calibers, thereby greatly saving the machining process.
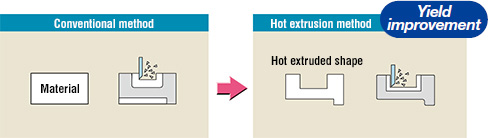
Save the Welding Process
Because hot extruded shapes are produced by means of solid forming, the welding processes can be saved. Further, stress relief can be saved, whereby thermal deformation during welding, thereby contributing greatly to cost cutting. In addition, the quality deterioration of weld portion can be prevented and the reliability of end products can be improved.
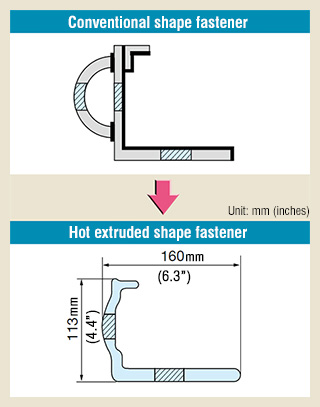
Suitable for Small-lot Production and Model Changes of Shapes
The cost of hot extrusion tools is much lower than that of rolling mill tools (rolls): Accordingly, the hot extrusion process allows not only the minor dimensions changes of each product to be altered simply by changing tools, but also the production of small lots starting at one-ton units that otherwise are economically untenable for rolling processes.
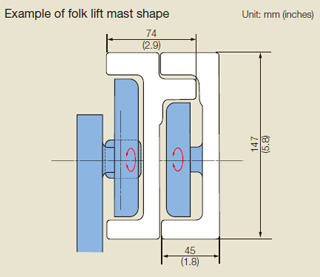
Catalog
Hot Extruded Steel Shapes The Tools of Free Design (4.26MB)
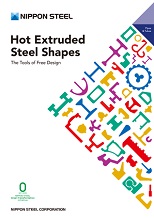
- introduction
- Features of Hot Extrusion Process
- Merit of Hot Extruded Shapes
- Application Example
- Configurations and Application Examples
- In Placing Orders
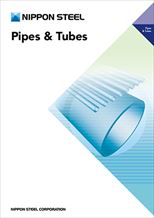
- Integrated Steel Manufacture
- Pipe-making facilities and product types
- NIPPON STEEL product standards
- Applications
- Pipes & tubes for piping
- Pipes & tubes for mechanical structures
- Pipes & tubes for marine structures and general structures
- Pipe piles/pipe sheet piles
- Pipes & tubes for shipbuilding
- Pipes & tubes for plants
- Pipes & tubes for boilers/heat exchangers
- Pipes & tubes for high pressure hydrogen
- Pipes & tubes for the chemical industry/nuclear power plant
- Oil & Gas Casing & Tubing/Line pipe (offshore)
- Production process
- Seamless pipes & tubes (Mannesmann process)
- Seamless pipes & tubes (hot extrusion・hot hollow forged)
- Electric resistance-welded pipes & tubes
- Hot electric resistance-welded pipe & tubes
- Arc-welded pipes & tubes
- Secondary machining
- Pipe & tube plant of NIPPON STEEL
Contact Information
For further product information
Product Quotes, and inquiries without complete information required in inquiry form may not be responded to. Selection of inquiries for reply online is at the sole discretion of NIPPON STEEL. We appreciate your understanding.