News
- Apr. 18, 2025 The civil engineering package has been updated with the addition of “Hat+H (Hat-type sheet pile for Deep excavation)” and “STEEL PIPE PILES with ribs x Sat-in Pile Foundation”.
- Apr. 02, 2025 Designing Metal TranTixxii to be Used in the Largest Quantity in the World on Taiwanese Temple Roof
- Mar. 10, 2025 Nippon Steel Obtained SuMPO EPD Certifications for Pipes and Tubes Used in Chemical Industry and for Boilers
- Dec. 12, 2024 Titanium with Aesthetic Appearance “TranTixxii” Service Life Warranty Launch —Launch of a maximum 150-year warranty through additional extensions—
- Oct. 31, 2024
Launch of the overseas version of ProStruct™, a solution brand for the construction industry
—Expanding the packaged series of steel materials and solution technology to overseas construction markets— - Oct. 30, 2024 Participation in the Japan Pavilion at ADIPEC, the Energy-Related Exhibition in the Middle East
- Oct. 07, 2024 Nippon Steel Obtained SuMPO EPD (Formerly EcoLeaf) Certificationsfor Its Hot Extruded Steel Shapes
- Jul. 10, 2024 Long-term OCTG supply contract with Aker BP renewed –Strengthens strategic partnership through stable supply of OCTG–
- Jul. 03, 2024 Long-term OCTG supply contract with Equinor renewed –Strengthens strategic partnership through stable supply of OCTG–
- Jun. 14, 2024 Acceptance of Orders for High-Alloy Seamless OCTG and Employment of Green Steel “NSCarbolex Neutral” Finalized for CCS to Be Used in Construction Project for Blue Ammonia Manufacturing Plant in the State of Qatar
- May. 15, 2024 Adoption of Coating Cycle Extension Steel “CORSPACE” for the First Time in Overseas ODA Bridge Construction
- Apr. 23, 2024 Participation in OTC, an Energy-Related Exhibition in the U.S.
- Mar. 22, 2024 Designing Titanium TranTixxii wins the European “iF DESIGN AWARD 2024” —The world's first non-ferrous metal material to receive the award—
- Sep. 28, 2023 The Adoption of “NSCarbolex Neutral” steel product for geothermal project in the Netherlands operated by 85 Degrees Renewables.
- Mar. 11, 2022 Nippon Steel's TranTixxii and NIPPON STEEL Stainless Steel Corporation's NSSC220M featured on the roof of an international conference center in Jiangsu, China
- April 22, 2021 Nippon Steel to Launch ZAM®-EX high corrosion resistant coated steel sheets for overseas markets
- Oct. 01, 2020 Our new product "FeLuceTM" (hairline-finished electroplated steel sheet) wins the Good Design Award 2020 ~Our first steel sheet to win the Good Design Award~
- Feb. 14, 2019 NSSMC Receives Shell’s Supplier Award
- Jul. 30, 2018 Execution of Strategic Partnership with BP Oman
- Jul. 30, 2018 "The beauty of distinctive gradations make people feel nature" was posted.
- Jul. 26, 2018 VAM® 21 HT CLEANWELL® DRY ST First Running
- Jul. 19, 2018 Steel Wires Joint Venture Company for Cold Heading and Forging in USA (NSCI) holds an Opening Ceremony
- Jun. 27, 2018 NSSMC and Standard Steel Receive TTX “Excellent Supplier 2017” Award
- May. 29, 2018 NSSMC Named a Top 100 Global Innovator in 2017 for Sixth Consecutive Year
- Apr. 25, 2018 Steel Wires Joint Venture Company for Cold Heading and Forging in USA (NSCI) Starts Commercial Production
- Apr. 17, 2018 Strengthening Supply System for Ultra-high-tensile Steel Sheets New CGL to be installed at Kimitsu Works
- Feb. 27, 2018 Nippon Steel & Sumikin Crankshaft, NSSMC’s manufacturing and sales subsidiary of crankshafts in the U.S., earns Diamond Supplier Award from Navistar
- Aug. 04, 2017 NSSMC’s proprietary titanium product TranTixxii™ is adopted for cladding of a theater in Jiangsu Province, China
Crankshafts and front axle beams
We have a proud tradition of manufacturing die-forged products since the founding of us. Our production facilities include the largest mechanical press in the world, our 16,000-ton high-speed forging press line, a 10,000-ton high-speed forging press line, a 6,500-ton high-speed automatic forging press line, a 5,000-ton high-speed automatic forging press line, and a 35-ton-meter hammer line, a 50-ton-meter hammer line. We use these facilities to manufacture approximately 4 million crankshafts annually. The proprietary manufacturing technologies that we have established are also highly evaluated by our many customers.

Characteristics
Superb manufacturing technology and facilities
We have a variety of forging, heat treatment and testing facilities for all types of applications. All the products produced with these facilities are guaranteed to be state-of-the-art and of consistent quality.
High dimensional accuracy
Using high-precision forging presses, we can provide products with high dimensional accuracy, even for complex shapes.
Integrated quality control system
Using high-quality steel supplied by our own steel works, all processes are conducted under an integrated quality control system, right up to delivery of the products.
Selection of optimum material for each application
Using our own steel for all products, we can select the best-suited material for each application.
CAE-driven product design
We can provide CAE-based design evaluation technology to assist customers with their product design.
Well-developed functional evaluation technology
We can make various evaluations of the crankshafts, including single-component fatigue tests, material tests and so on.
Production range
Major products | Weight [kg] | Overall length [mm] |
---|---|---|
Crankshafts | 5 to 2000 | 300 to 3000 |
Front axle beams | 30 to 150 | 700 to 2000 |
Aircraft landing gear | 35 to 500 | − |
We can manufacture various sizes of crankshafts for use from automobiles to industrial machinery.
Explore
Crankshafts for passenger cars

Crankshafts for trucks and buses

Front axle beams
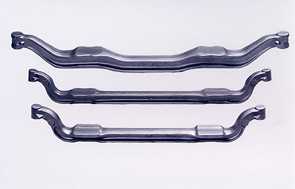
Landing gear for aircraft

Contact Information
For further product information
Product Quotes, and inquiries without complete information required in inquiry form may not be responded to. Selection of inquiries for reply online is at the sole discretion of Nippon Steel. We appreciate your understanding.