News
- Apr. 18, 2025 The civil engineering package has been updated with the addition of “Hat+H (Hat-type sheet pile for Deep excavation)” and “STEEL PIPE PILES with ribs x Sat-in Pile Foundation”.
- Apr. 02, 2025 Designing Metal TranTixxii to be Used in the Largest Quantity in the World on Taiwanese Temple Roof
- Mar. 10, 2025 Nippon Steel Obtained SuMPO EPD Certifications for Pipes and Tubes Used in Chemical Industry and for Boilers
- Dec. 12, 2024 Titanium with Aesthetic Appearance “TranTixxii” Service Life Warranty Launch —Launch of a maximum 150-year warranty through additional extensions—
- Oct. 31, 2024
Launch of the overseas version of ProStruct™, a solution brand for the construction industry
—Expanding the packaged series of steel materials and solution technology to overseas construction markets— - Oct. 30, 2024 Participation in the Japan Pavilion at ADIPEC, the Energy-Related Exhibition in the Middle East
- Oct. 07, 2024 Nippon Steel Obtained SuMPO EPD (Formerly EcoLeaf) Certificationsfor Its Hot Extruded Steel Shapes
- Jul. 10, 2024 Long-term OCTG supply contract with Aker BP renewed –Strengthens strategic partnership through stable supply of OCTG–
- Jul. 03, 2024 Long-term OCTG supply contract with Equinor renewed –Strengthens strategic partnership through stable supply of OCTG–
- Jun. 14, 2024 Acceptance of Orders for High-Alloy Seamless OCTG and Employment of Green Steel “NSCarbolex Neutral” Finalized for CCS to Be Used in Construction Project for Blue Ammonia Manufacturing Plant in the State of Qatar
- May. 15, 2024 Adoption of Coating Cycle Extension Steel “CORSPACE” for the First Time in Overseas ODA Bridge Construction
- Apr. 23, 2024 Participation in OTC, an Energy-Related Exhibition in the U.S.
- Mar. 22, 2024 Designing Titanium TranTixxii wins the European “iF DESIGN AWARD 2024” —The world's first non-ferrous metal material to receive the award—
- Sep. 28, 2023 The Adoption of “NSCarbolex Neutral” steel product for geothermal project in the Netherlands operated by 85 Degrees Renewables.
- Mar. 11, 2022 Nippon Steel's TranTixxii and NIPPON STEEL Stainless Steel Corporation's NSSC220M featured on the roof of an international conference center in Jiangsu, China
- April 22, 2021 Nippon Steel to Launch ZAM®-EX high corrosion resistant coated steel sheets for overseas markets
- Oct. 01, 2020 Our new product "FeLuceTM" (hairline-finished electroplated steel sheet) wins the Good Design Award 2020 ~Our first steel sheet to win the Good Design Award~
- Feb. 14, 2019 NSSMC Receives Shell’s Supplier Award
- Jul. 30, 2018 Execution of Strategic Partnership with BP Oman
- Jul. 30, 2018 "The beauty of distinctive gradations make people feel nature" was posted.
- Jul. 26, 2018 VAM® 21 HT CLEANWELL® DRY ST First Running
- Jul. 19, 2018 Steel Wires Joint Venture Company for Cold Heading and Forging in USA (NSCI) holds an Opening Ceremony
- Jun. 27, 2018 NSSMC and Standard Steel Receive TTX “Excellent Supplier 2017” Award
- May. 29, 2018 NSSMC Named a Top 100 Global Innovator in 2017 for Sixth Consecutive Year
- Apr. 25, 2018 Steel Wires Joint Venture Company for Cold Heading and Forging in USA (NSCI) Starts Commercial Production
- Apr. 17, 2018 Strengthening Supply System for Ultra-high-tensile Steel Sheets New CGL to be installed at Kimitsu Works
- Feb. 27, 2018 Nippon Steel & Sumikin Crankshaft, NSSMC’s manufacturing and sales subsidiary of crankshafts in the U.S., earns Diamond Supplier Award from Navistar
- Aug. 04, 2017 NSSMC’s proprietary titanium product TranTixxii™ is adopted for cladding of a theater in Jiangsu Province, China
Test Equipment
We supply a wide range of test equipment such as machines to test axle bending under varying loads, fatigue test machines, and high-speed brake testing machines.
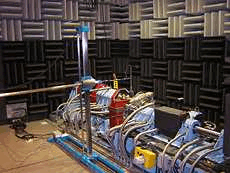
Variable load rotational bending fatigue tester for railcar axles
Outline
It is very important to accurately assess the actual strength of axles to make them both adequately safe and lightweight. Due to test equipment limitations, fatigue testing on actual axles has been conducted under fixed amplitude loads. However, the loads on actual cars constantly fluctuate, and it would be difficult to say that actual conditions have been recreated in those tests. Therefore, a new tester, capable of simulating variable load conditions closer to actual operation, was introduced in 1995 to replace the conventional fixed -load rotational bending fatigue tester.
Characteristics
- Testing simulating actual conditions
- We can verify the fatigue strength of axles, including the fitted parts, by assembling test wheels and a test axle that matches an actual axle.
- Testing by automatic control
- Tests can be conducted at maximum loads of up to 157kN, and programming the conditions allows for long-term unattended operation testing.
High-speed brake tester for railcars
Outline
With the increasing speed of trains, the need to investigate high-speed braking performance of brake disks for railway applications has increased. Therefore, we introduced a high-speed brake test machine in 2001 in addition to our conventional tread and disk brake test equipment. In addition to brake testing at the equivalent of up to 600km/h, this machine also handles basic brake performance tests and durability tests, as well as run-curve test conditions similar to those in an actual car, with controlled brake torque and deceleration rate.
Characteristics
- Brake testing compatible with increased speeds
- Brake testing is possible at maximum speeds of 600km/h (with a wheel diameter of 860mm), making it possible to perform high-speed compatible brake performance and durability testing. (16 ton-equivalent severe-load brake testing is also possible at 400km/h with a wheel diameter of 860mm)
- Various brake control tests (run-curve)
- Brake tests are also possible with constant torque control and constant deceleration rate control, making it possible to conduct brake tests under conditions similar to those in actual operation, taking grade, run-curve, running wind, etc. into consideration. Test data, such as average friction coefficient and torque can also be automatically recorded.
High-speed loaded spin test equipment exclusively for railcar drive units
Characteristics
- High-speed compatible
- We have achieved maximum test speeds of 500km/h (200km/h faster than our conventional test performance), making the testing equipment compatible with high-speed train development.
- Evaluation under actual car torque loads
- In the past, performance was verified by running tests on actual cars after the cars had been completed. With this testing equipment, characteristics can be simulated under actual torque load conditions.
- Analysis and predictive design of acoustic characteristics
- By employing a semi-anechoic chamber and an axel and pinion shaft drive system, we can now analyze the noise sources and acoustic characteristics from the drive unit itself, without any disturbance from other noise sources, facilitating more accurate predictive design.
Railcar bogie spin testing rig
Outline
High-speed railway systems such as the Shinkansen have drawn attention from the viewpoints of environmental and energy issues. At the same time, much higher speeds are being pursued. The bogie spin testing rig has rotating rail-wheels that correspond to rails, on which a load frame, which corresponds to an actual car body, is set. This allows the various problems that arise when a railcar is running at high speeds, such as running instability, to be worked out in advance.
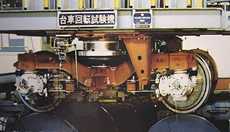
Characteristics
- High-speed compatible testing
- Having attained a maximum test speed of 500km/h, we can conduct running-stability validation tests that are compatible with the future development of high-speed performance.
- Evaluation under actual car torque loads
- In the past, performance was verified by running tests on actual cars after the cars had been completed.
With this testing equipment, characteristics can be simulated under actual torque load conditions. - Testing for all types of bogies
- The track gauge and axle center-distance are all variable on the test machine to enable testing of a variety of bogies.
Fatigue test equipment for railcar bogies
Outline
Railcar bogies must meet extremely high standards. It is also important that they are lightweight. Using the bogie fatigue tester, we can conduct strength assessment tests to check long-term serviceability by applying repetitive loads that simulate actual usage conditions of real bogies.
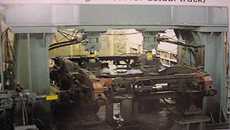
Characteristics
- Testing under various load conditions
- Testing can be conducted under various load conditions, such as several sine wave and rectangular wave load waveforms, and load waveforms that simulate actual conditions.
- Evaluation under actual car torque loads
- In the past, performance was verified by running tests on actual cars after the cars had been completed.
With this testing equipment, characteristics can be simulated under actual torque load conditions. - Testing by automatic control
- Fatigue testing under long-term unattended operating conditions can be conducted by automatic control.
Contact Information
For further product information
Product Quotes, and inquiries without complete information required in inquiry form may not be responded to. Selection of inquiries for reply online is at the sole discretion of Nippon Steel. We appreciate your understanding.