スチール製超軽量クロージャー部品の開発成果を更新
2001/05/28
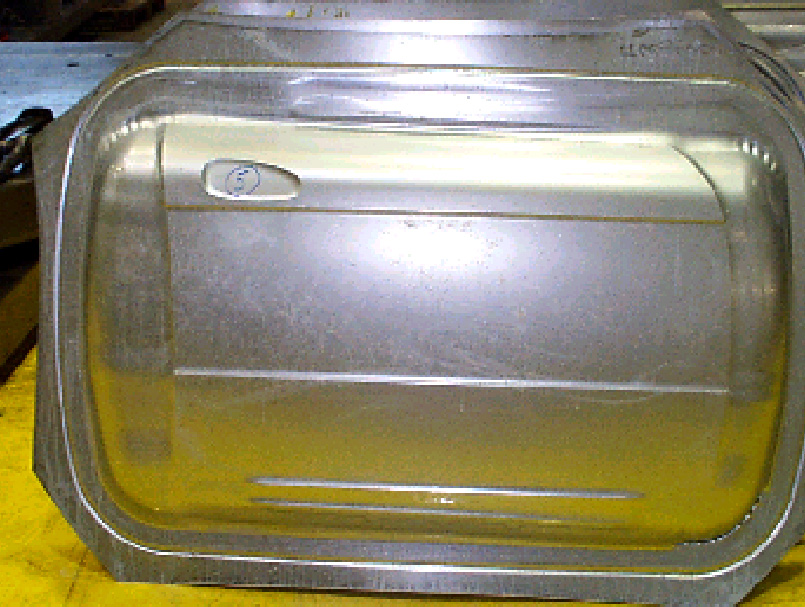
シートハイドロフォーム後のドア外板
高強度鋼板とシートハイドロフォームの組合せで車のクロージャー部品がさらに軽量化できるとULSACコンソーシアムが23日明らかにしました。厚さ0.6mm、強度600MPaのDP(Dual Phase)鋼とシートハイドロフォームを用いて、ドアの外板を製造することに成功しました。
IISI(国際鉄鋼協会)が中心となり世界の主要鉄鋼会社35社が共同で推進したULSAB(UltraLight Steel Auto Body)プロジェクトは、スチール製車体で車体性能・衝突安全性を確保しつつ、コスト増なしで25%の軽量化が可能であることを実証しました。ULSAC(UltraLight Steel Auto Closures)ではクロージャー部品の軽量化をULSABと同様、IISIのプロジェクトとして世界の鉄鋼会社がPorsche Engineering Service社と共同で進め、昨年5月に試作ドアを発表しました。前回プレスにより製造した外板を、今回はシートハイドロフォームにより製造することで外板を0.1mm薄くでき、ドア重量をさらに軽量化できました。
ULSACプログラムはドア、フード、デックリッド、ハッチの軽量設計を行う設計段階を経て次の実証段階で軽量ドアを試作しました。このときのドアの外板は厚さ0.7mmの390MPa焼付強化鋼をプレスで製造しドアの重量は10.47kgでベンチマークに比べて33%軽くできました。
プレス成形された外板は、車のスタイルにもよりますが部品の中央部分の引張りが不足し十分な加工硬化が得られません。従って耐デント性等を改善するためには材料の厚みを増す必要があり重量が重くなります。シートハイドロフォームでは下型が液体であるので型内での材料の延びを制限する摩擦がありません。このため外板中央部に加工硬化により十分な強度が与えられ軽量化しても耐デント性とオイルキャニング(ぺコツキ)性能が維持されます。試作ドアの性能テストでは剛性、側面衝突に対する強度が確認されました。またコンピューター解析により完成車の前方衝突時のエネルギー吸収に貢献することも分かりました。
今回のドアは9.77kgと前回より0.7kg軽くなりベンチマークからは37%軽くできました。またコスト解析によると年間22.5万台製造時にはシートハイドロフォーム製外板はプレス製より3.72ドル高く、軽量化のために若干のコスト増が発生しました。ハイドロフォームはプレスと比較して能率が低いためです。能率の向上はコスト競争力を上げるキーです。
以上の詳細はULSACのホームページwww.ulsac.orgにあるEngineering Reportに公開される予定です。また今回試作したドアは鉄鋼会館(東京都中央区日本橋茅場町3)において近日中に展示される予定です。
(連絡先)新日本製鐵 技術開発企画部 大橋 03-3275-7974