Cracks products and reduces CO2 and processes in manufacturing.

Steel optimized for the customer's method x customer's products with high strength.
We developed steel for cracking connecting rod, which is manufactured by cracking steel products after integrally molding rod and cap parts.
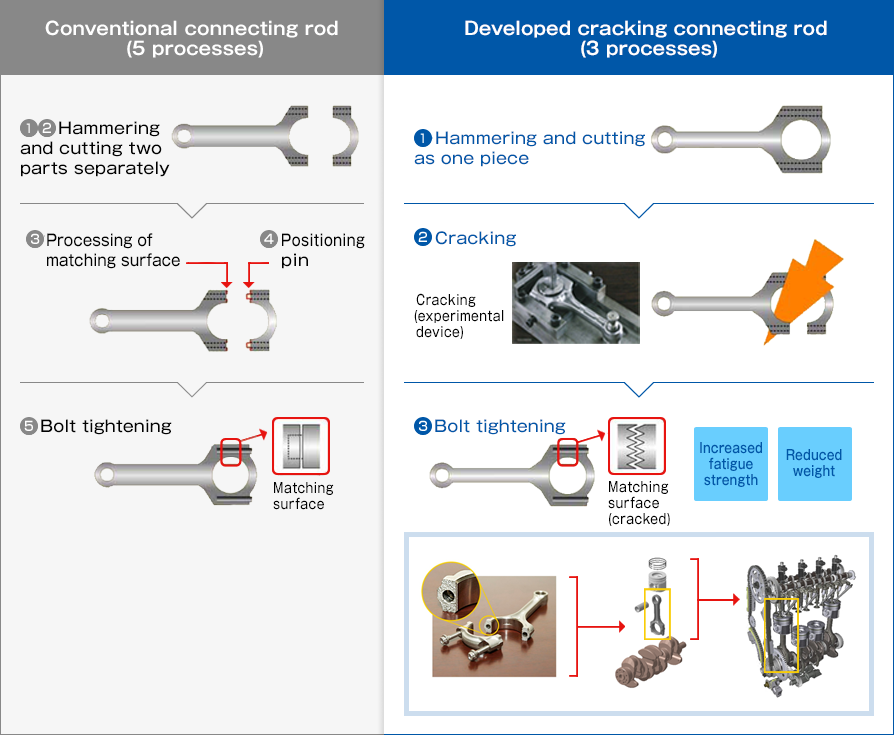
Pursuit of the highest potential of steel (high strength, material that can be cracked)
①The cracking method simplifies the manufacturing process of connection rod (omits two processes from the conventional method).
②Enhances the fatigue strength of the material and prevents weakening of the conflicting workability.
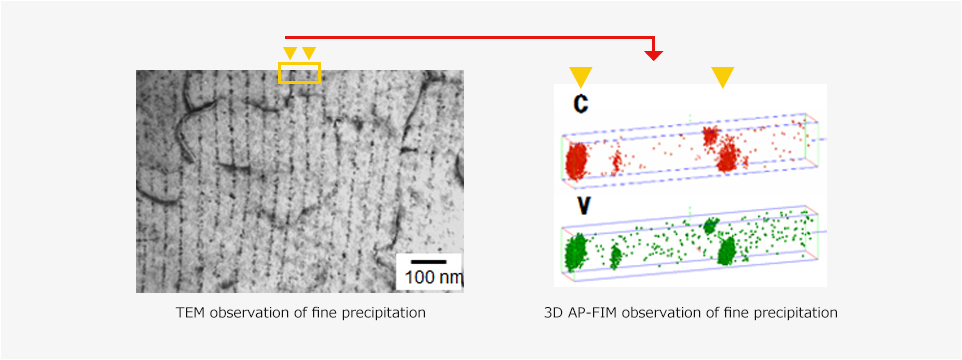
The new material provides excellent cracking capability. Despite confliction, it realized practical workability using a non-lead component.
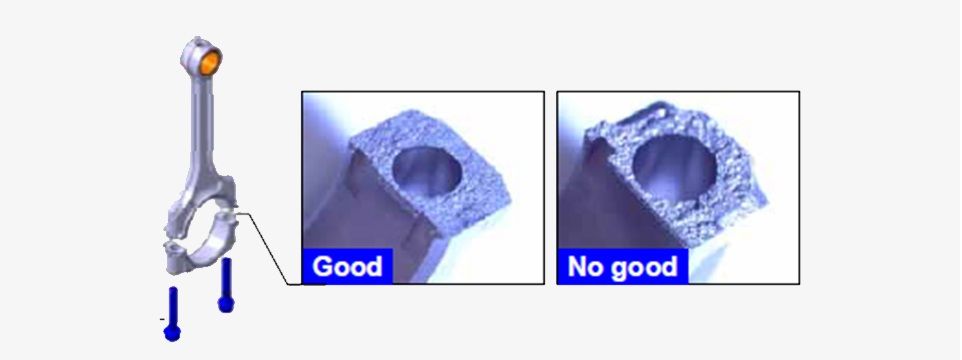
- Award history:2006 Prize of Excellence and Appreciation by Honda Motor Co., Ltd.
2007 Prize of Technology Development by the Japan Institute of Metals and Materials
2009 Special Prize of the Monozukuri Nihon Grand Award
- This video was created by the Japan Machinery Federation.
- The company name "Sumitomo Metals KOKURA," which was used at the time of filming, was replaced by the current Kyushu Works Yawata area of NIPPON STEEL.