TOUGH GUARD™ and its series line-up
What is TOUGH GUARD™?
Nippon Steel's newly-developed plated wire coated with three coating elements: zinc, aluminum and magnesium.
Characteristics
- Holds about 5 times more corrosion resistance than the conventional zinc aluminum alloy.
- Based on the corrosive loss evaluation by plate type in 5,000 hours of salt water spraying.
List of TOUGH GUARD™ series
Product name |
Plating technology |
Base material |
Plate surface |
Purpose of use |
TOUGH GUARD™ FROST
TGF |
Three coating elements of zinc, aluminum and magnesium
*Common in TOUGH GUARD™ series |
Soft steel wire rod |
Rough |
Wire mesh for bank protection |
TOUGH GUARD™ MILD
TGM |
Smooth |
Fence, etc. |
TOUGH GUARD™ HARD
TGH |
Hard steel wire rod |
Power transmission/distribution lines, suspension wire for railway |
What is TOUGH GUARD™ FROST (TGF)?
Developed exclusively for a base material of wire mesh for river bank protection.
This material prevents slippage with the rough surface using soft steel wire rod.
This product is sold by Nippon Steel.
What is TOUGH GUARD™ MILD (TGM)?
Excellent in bending workability and corrosion resistance in welding parts, this can be used for fences.
Soft steel wire rod is used and the surface has no rough coating.
This product is developed by Nippon Steel and manufactured and sold by NS Hokkai Seisen and Nichia Steel Works.
What is TOUGH GUARD™ HARD (TGH)?
Used mainly for railway, power transmission/distribution lines and communication fields.
Plated steel wires with high corrosion resistance and steel stranded wires using hard steel wire rod.
Nippon Steel and J-WITEX jointly developed TOUGH GUARD™ HARD based on the TOUGH GUARD™ technology of Nippon Steel.
Assumed purposes of use
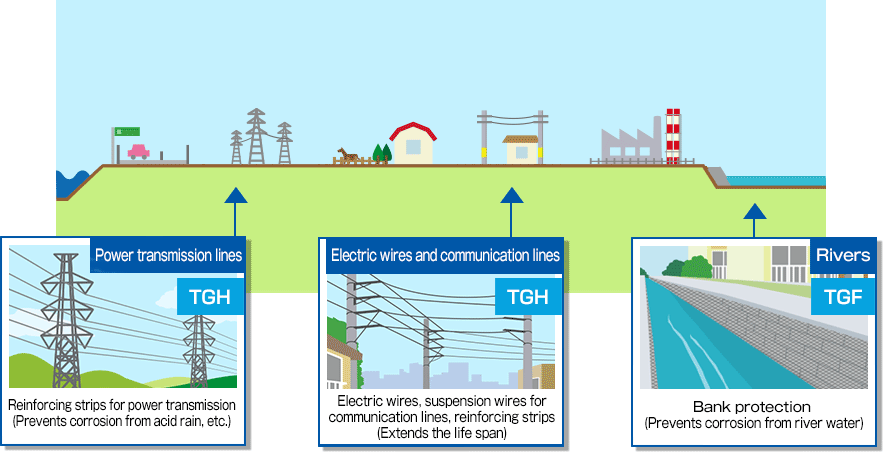
Advantages of customers
-
1
Enables reduction of life cycle costs with the high corrosion resistance*
- Data on high corrosion resistance is shown at the bottom of the page.
-
2
Longer life span and reduced costs are expected if replaced by other materials (resin, aluminum, stainless).
Corrosion resistance evaluation data
Corrosion resistance evaluation (salt water spraying test)
corrosive loss evaluation was conducted through the test based on JIS (Z2371 rule).
(See Table 1 for test conditions)
Evaluation results (relationship between the length of salt water spraying and corrosive loss)
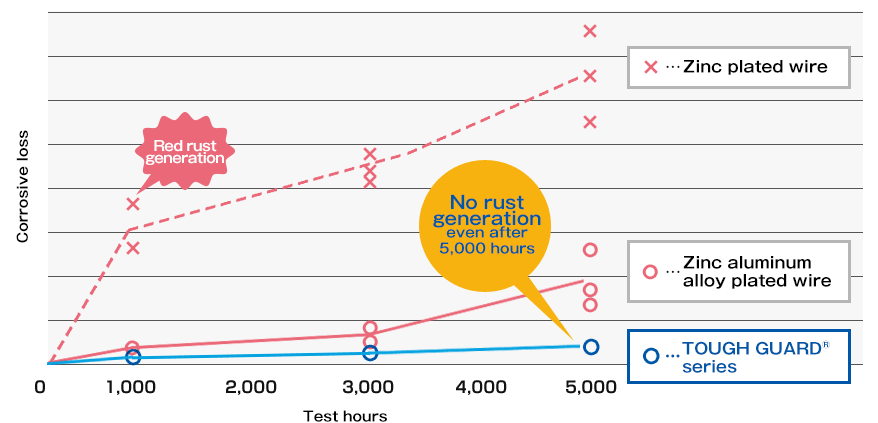
Evaluation results (relationship between the length of salt water spraying and corrosive loss)
This can be used for a wide range of purposes such as wire mesh, as it is excellent in corrosion resistance in bent and welded parts.
Results of salt water spraying test (3,000 hours)
Results of salt water spraying test (5,000 hours)
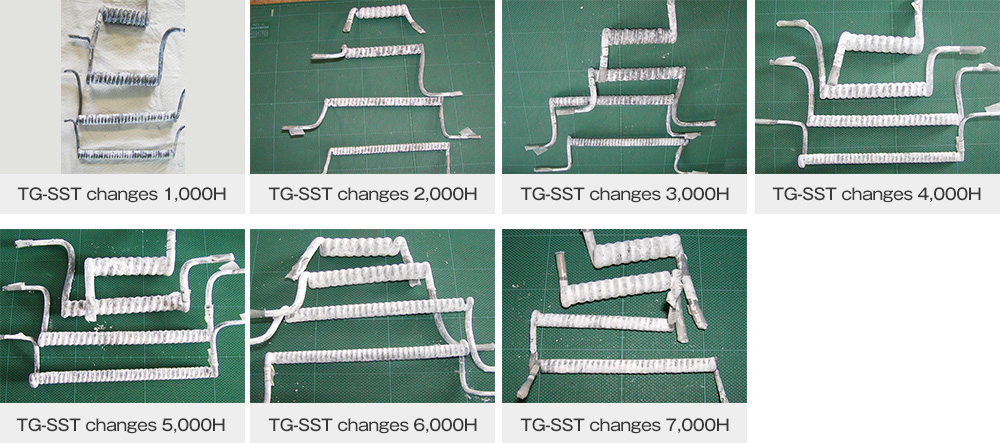